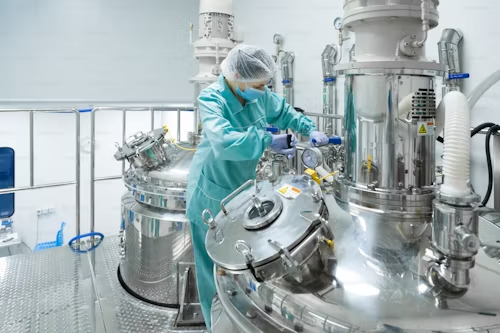
In the fermentation manufacturing industry, fermenters are one of the core pieces of equipment, especially in the chemical engineering, pharmaceutical, and food industries. Among them, the batch reactor plays a crucial role in the product manufacturing process as an efficient reaction device. This article will introduce the key technical features of batch reactors, selection guidelines, and how to choose the most suitable equipment based on different needs, helping manufacturers optimize production processes and improve product quality.
What is a Batch Reactor?
A batch reactor is a closed device used for chemical reactions. The working principle involves placing reactants into the reactor in specific proportions, after which the instrument is activated, and the entire reaction process is completed within a set time frame. Unlike continuous reactors, reactors are typically suited for production scenarios with smaller demands and high batch requirements. Due to its strong operational flexibility and precise process control, it is widely used in chemical synthesis, pharmaceuticals, food processing, and other industries.
5T industrial batch bioreactor fermenter
Advantages of Batch Reactors
- Precise Process Control
Batch reactors offer high levels of process control, allowing for precise adjustments of key reaction parameters, such as temperature, pressure, reaction time, and stirring speed. This high level of adjustability enables them to meet the varying production needs of different products, ensuring consistent quality for each batch and reducing fluctuations and deviations in production. Whether dealing with temperature-sensitive reactants or processes that require strict timing control, Batch reactors provide reliable control to optimize product quality and production efficiency. - Strong Adaptability
Batch reactors demonstrate excellent adaptability in various production environments. They are suitable for producing a wide range of products, especially in cases where demand fluctuates. Compared to continuous reactors, Reactors can handle diverse raw materials and flexibly adjust production batch sizes based on demand. This makes them an ideal choice for manufacturers facing market demand fluctuations or changes in product types. Whether for regular product production or small batch custom manufacturing, Batch reactors efficiently meet diverse needs. - Ideal for Small-Batch Production
For companies that produce smaller-scale and diverse products, batch reactors are particularly well-suited for small-batch production. Compared to other reactors, it is more cost-effective when handling small batches. In scenarios where product variety is high and production batch sizes are small, using a batch reactor helps minimize equipment investment and reduces material waste. Their efficient operation allows manufacturers to meet varying market demands without incurring additional costs, especially for custom or high-value-added product production, providing excellent cost performance. - Lower Energy Consumption
Batch reactors also have a significant advantage in terms of energy efficiency. Their design allows for precise control of temperature and pressure during the reaction process, minimizing energy waste. During production, reactors typically adjust energy input based on real-time feedback, avoiding excessive heating or cooling and optimizing energy usage efficiency. For reactions that require long operation times, batch reactors’ energy-saving performance is especially notable, helping companies reduce energy consumption while maintaining production efficiency and lowering costs.Bailun industrial batch bioreactor
Key Factors to Consider When Choosing a Batch Reactor
For manufacturers, selecting the right batch reactor to meet production needs is crucial. The following factors are particularly important when making a purchase decision:
- Production Capacity: Choose a reactor that matches the production scale of the company to ensure it can efficiently complete the intended production tasks. The reactor’s volume and reaction rate are key factors affecting production capacity.
- Control Requirements of the Reaction Process: If the reaction process requires strict control of temperature and pressure, choosing a reactor with an advanced control system will help ensure product quality.
- Material and Corrosion Resistance: The material of the batch reactor should be selected based on the properties of the reactants. For certain chemical reactions, a reactor material that is resistant to high temperatures and corrosion, such as stainless steel or high-alloy materials, may be necessary.
- Degree of Automation: With the advancement of Industry 4.0, the application of automation control systems is becoming more widespread. Selecting a bioreactor equipped with automated monitoring and adjustment systems can significantly improve production efficiency and safety.
Five-stage-5L glass bioreactor
How to Select the Right Batch Reactor Based on Specific Needs?
- Small-Scale Experimental Production: For new product development or small trial production runs, it is recommended to choose a batch reactor of moderate size with easy operation. These reactors are typically moderately priced and offer flexible process adjustment capabilities.
- Large-Scale Production: For large-scale manufacturers, it is crucial to choose a highly efficient batch reactor with a higher degree of automation. Such equipment can reduce production costs while ensuring quality.
- Special Material Reactions: If the reaction process involves highly corrosive, high-temperature, or other special requirements, a reactor with corrosion-resistant and high-temperature resistant features should be selected.
Industry Trends and Technological Developments
With the acceleration of smart manufacturing and digital transformation, batch reactor technology is continuously evolving. In recent years, many devices have been equipped with advanced process control systems, making the production process more efficient and controllable. Additionally, energy-saving and emission reduction have become key factors to consider when choosing equipment. Reactors with high energy efficiency and low resource consumption are among the best-selling products on the market.
Green production has become one of the main goals for manufacturers, and batch reactors can lower energy consumption and waste emissions while maintaining reaction efficiency. As the demand for sustainable development grows, more environmentally friendly reactors are being developed to meet market needs for eco-friendly production processes.
As a flexible and precise production device, the Batch reactor has become an indispensable part of modern manufacturing. By choosing the right equipment and implementing meticulous process control, manufacturers can significantly improve production efficiency and product quality. When purchasing a reactor, factors such as production scale, process requirements, degree of automation, and energy efficiency should be considered to help manufacturers make smarter decisions.
When selecting the most suitable batch reactor, it is essential to align the equipment with actual needs, industry trends, and technological advancements to maximize production efficiency and economic benefits. Choose our high-quality Batch reactor products to make your production processes more precise and efficient, taking your business to the next level.