1、 System design principles and composition
A biological process is the process in which a biological system undergoes biochemical reactions in a bioreactor. The bioreactor system and its surrounding environment form a relatively closed ecosystem. In this ecosystem, there are interactions between biological systems and environmental factors.
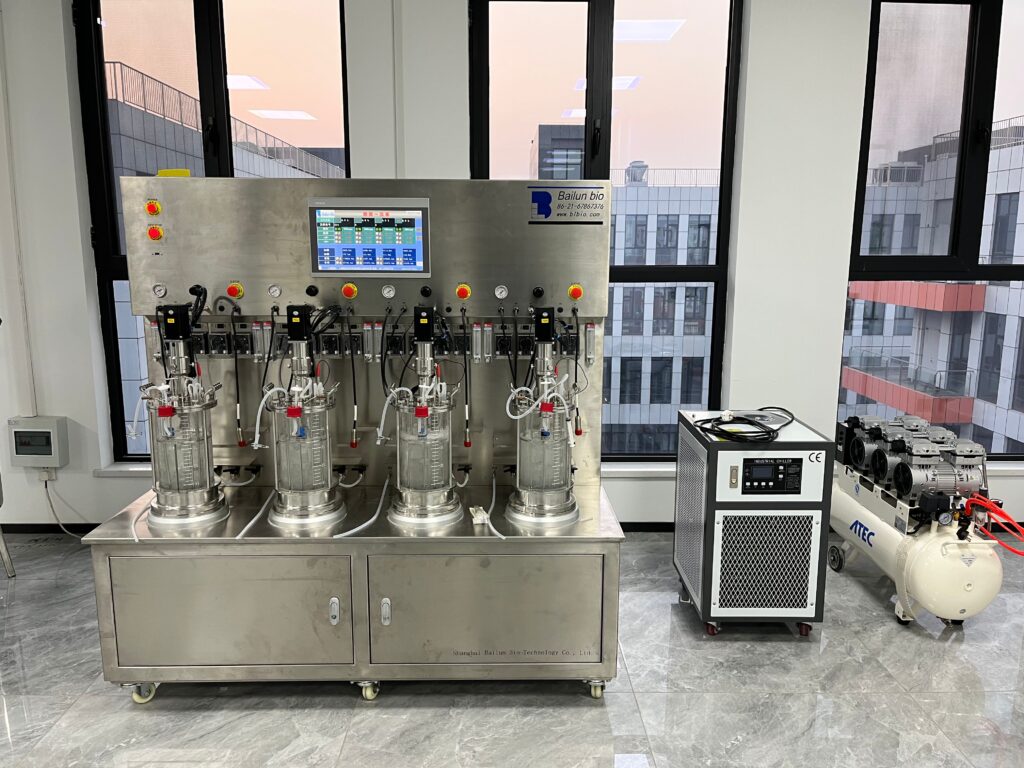
The phenotype of biological systems, especially those dominated by cells, is closely related not only to genotype, but also to the micro or macro environmental conditions in which the cells are located (such as nutrient types, pH, temperature, dissolved oxygen, mixing and transfer characteristics of bioreactors, etc.). In other words, genotype and environment jointly determine the phenotypic characteristics of biological systems. On the other hand, biological processes have highly nonlinear and time-varying characteristics, making it difficult to characterize their complex ontological features using macroscopic dynamics aimed at detecting and controlling environmental operating parameters.
Therefore, it is necessary to systematically analyze the metabolic changes of cells based on the metabolic characteristics related to parameters during the fermentation process, emphasizing that the physiological state of cells is related to parameters and is the result of the transfer, conversion, and balance of materials, energy, or information in bioreactors. Although its micro influencing factors may only occur at a certain scale at the level of genes, enzymes, cells, or reactors, they will ultimately be reflected in macro processes, providing clues for studying data correlation analysis methods at different scales in bioreactors.

An ideal bioreactor system should detect and analyze operating parameters and state parameters at different scales as much as possible, so as to potentially construct an optimized external environment that maximizes the gene expression and metabolic regulation of microorganisms for the biosynthesis of a certain target product and maximizes the accumulation of the target product.
The above indicates the engineering science issues of biological processes, which have evolved from macroscopic dynamics research to multi-scale theoretical methods based on biological process information processing, in order to guide the development of engineering technologies related to biological processes with bioreactor system as the core.
Bailun adopts a metabolic flow multi-scale biological reaction system, which includes various advanced sensors for the detection of cell physiological metabolic characteristics, sensor reactors and control systems for micro metabolic flow analysis of biological processes, computer software packages for the correlation analysis of cell physiological metabolic parameters, and computer Internet systems for data processing and remote analysis of fermentation processes.
This system is consistent with the highest configuration in Europe, reducing the interference of human factors on scientific research, improving data repeatability and accuracy, reducing labor and material costs, without the need for dedicated personnel on duty, and can achieve computer remote control and wireless monitoring.
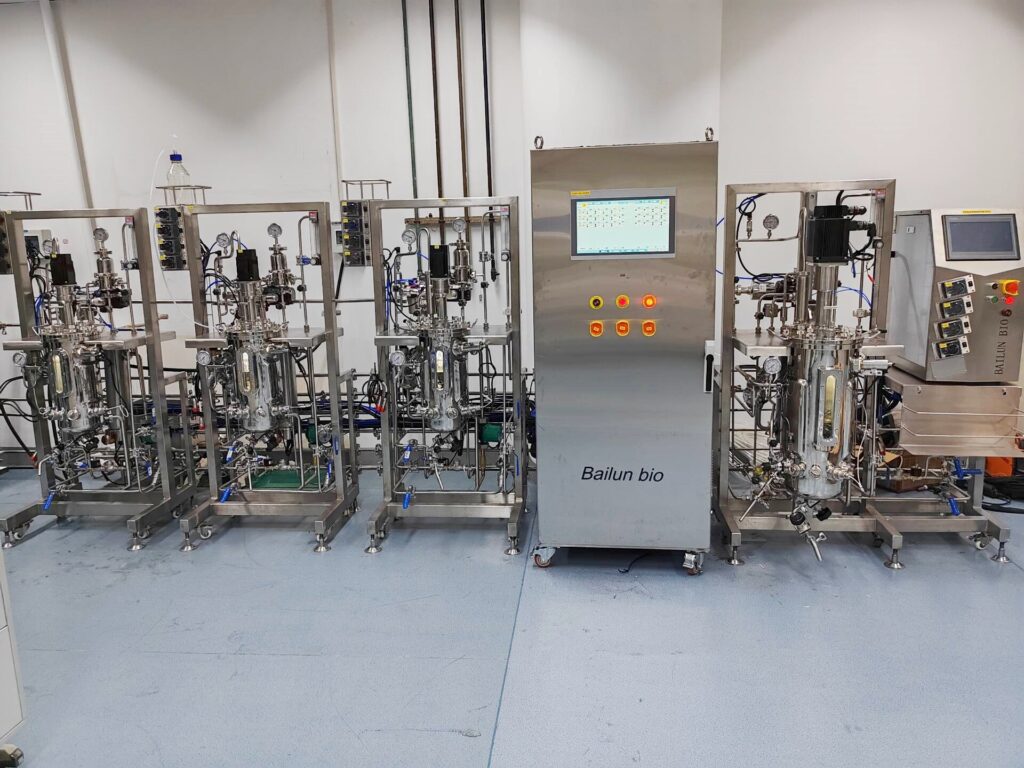
The can lid automatic opening system, and all parameters can be automatically controlled. Being able to obtain as much biological information as possible at various scales of the biological processing process, and then based on the principle of multi-scale parameter correlation, through real-time data processing of computer software, identifying key parameters for process optimization based on parameter correlation characteristics in massive data, and using them to guide process operations, equipment design, or strain screening and transformation, ultimately achieving process optimization and scaling up.
The system has been successfully applied to optimize the production process of various products, greatly improving the capacity of fermentation units. Its optimized process can generally be directly scaled up from tens of liters of fermentation tanks to industrial production fermentation tanks of hundreds of cubic meters.
2.Development and Application of Advanced Online Instruments
(1)Online sensors of bioreactor system
The bioreactor system with metabolic flow analysis as its core is equipped with advanced sensing systems. In addition to conventional detection and control parameters such as pH, temperature, stirring speed, dissolved oxygen, and rotor flow meter, a thermal mass flow meter (for precise measurement and control of intake flow rate to ensure it is not affected by intake pressure), a fermentation broth weighing system, exhaust gas oxygen and CO2 measuring instruments (exhaust gas composition analyzer or process exhaust gas mass spectrometer), and a top mounted silicone oil pressure sensor are also configured to accurately measure the oxygen consumption rate (OUR) and CO2 release rate (CER) of biological processes.
Micro metabolic flow analysis sensor reactors and control systems, in situ live cell concentration online measuring instruments, cell morphology online microscopic observation instruments, and other online sensors can also be configured as needed. Based on the direct parameters obtained from the measurement, important physiological and metabolic state parameters such as CER, OUR, and RQ can be calculated using computer software packages for cell physiological and metabolic parameter analysis.
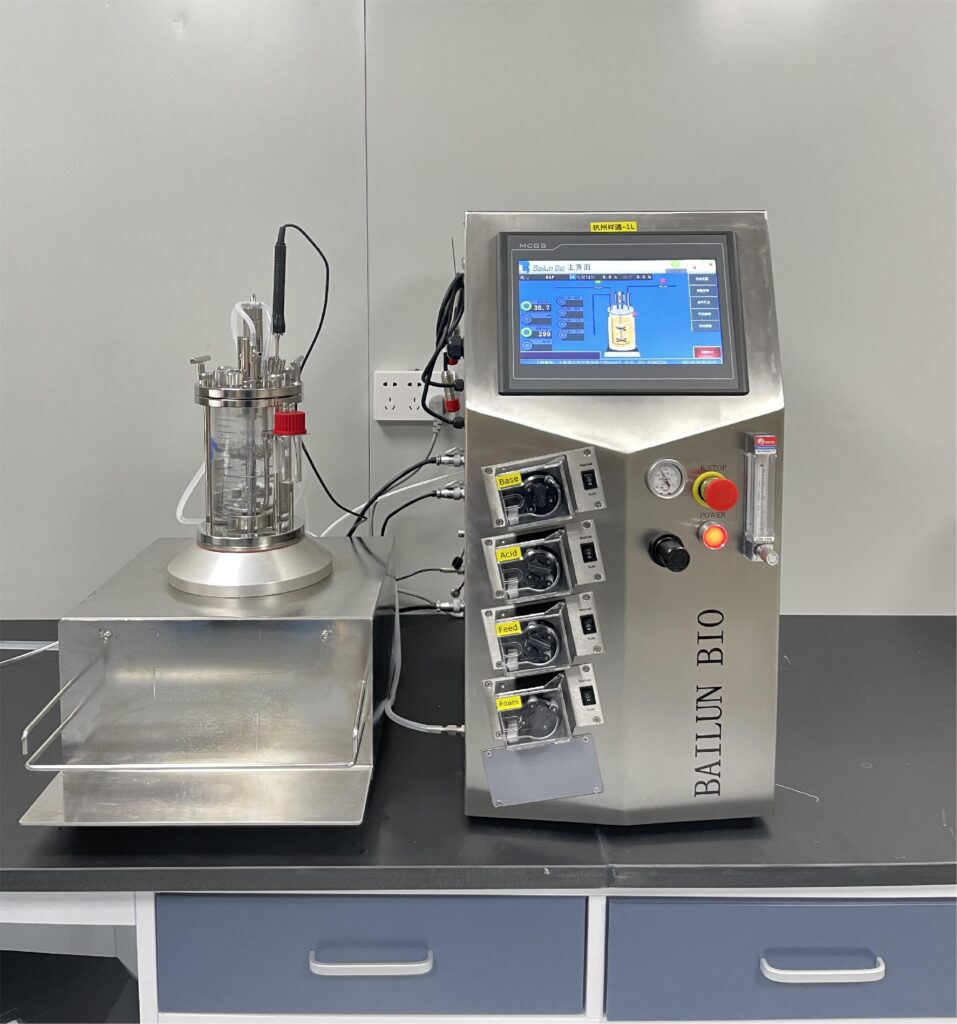
(2)Exhaust gas mass spectrometer of bioreactor system
The process exhaust gas mass spectrometer is mainly used for measuring the concentrations of O2, CO2, and N2 in exhaust gas. This mass spectrometer uses an electron bombardment ion source. After online pretreatment, the exhaust gases from different fermentation tanks are continuously input into the ionization chamber through a multi-channel rotary valve to form ions.
Using the motion law of charged particles in the electric field, the quadrupole mass analyzer separates the ions generated by the ion source according to their mass to charge ratio (mass to charge ratio, m/z), measures the distribution of ion mass intensity, and obtains information on compound types and concentrations, accurately reflecting changes in the composition of fermentation exhaust gases.
The measurement results can be input into a specialized software package designed for the fermentation process, enabling correlation analysis with other fermentation parameters. The exhaust gas mass spectrometer can measure volatile gas components with a relative molecular weight of up to 300, so it can also detect small molecule substances such as ethanol and methanol according to fermentation needs.
(3)Measurement analyzer of bioreactor system
Biomass is an important parameter in the fermentation process. At present, it is usually obtained through offline measurements using classic methods such as dry mass and turbidity. The in-situ live cell concentration online analyzer can not only perform real-time online measurement, but also obtain more biologically meaningful live cell concentrations.
This is particularly suitable for fermentation processes that contain insoluble solid substances in the culture medium. The principle of the live cell analyzer is based on 0 In an alternating electric field with a frequency range of 1-10MHz, non-conductive polarization occurs on the cell surface such as the cell membrane in the fermentation broth, making living cells with intact cytoplasmic membranes essentially like capacitors (the non-conductive nature of lipid cytoplasmic membranes generally leads to charge growth), while dead cells, lysed cells, cell fragments, bubbles, and other matrix components are essentially non polarizable.
By applying an alternating electric field within the frequency range using dual electrodes, the measured capacitance between the electrodes depends on the cell type and size, and is proportional to the concentration of viable bacteria within a certain range. The in situ live cell concentration online analyzer is applicable to various animal and plant cells, yeast, bacteria, algae, etc. But it is not suitable for fermentation processes that require acid-base neutralizing agents as the target product, as excessive ion strength in the fermentation broth can interfere with the accurate measurement of capacitance.
Micro bioreactor
The micro bioreactor system is a novel biochemical experimental platform that enables the study and control of biological reactions in small-scale reactors. This system combines the advantages of microfluidic technology, microelectronic devices, and biotechnology to perform the functions of traditional bioreactors at the microscale. Micro bioreactor systems typically consist of microfluidic chips, micro pumps, temperature control, and control systems. Microfluidic chips are core components composed of microchannels and microvalves, used to regulate the flow and mixing of microorganisms and substrates in reactors.
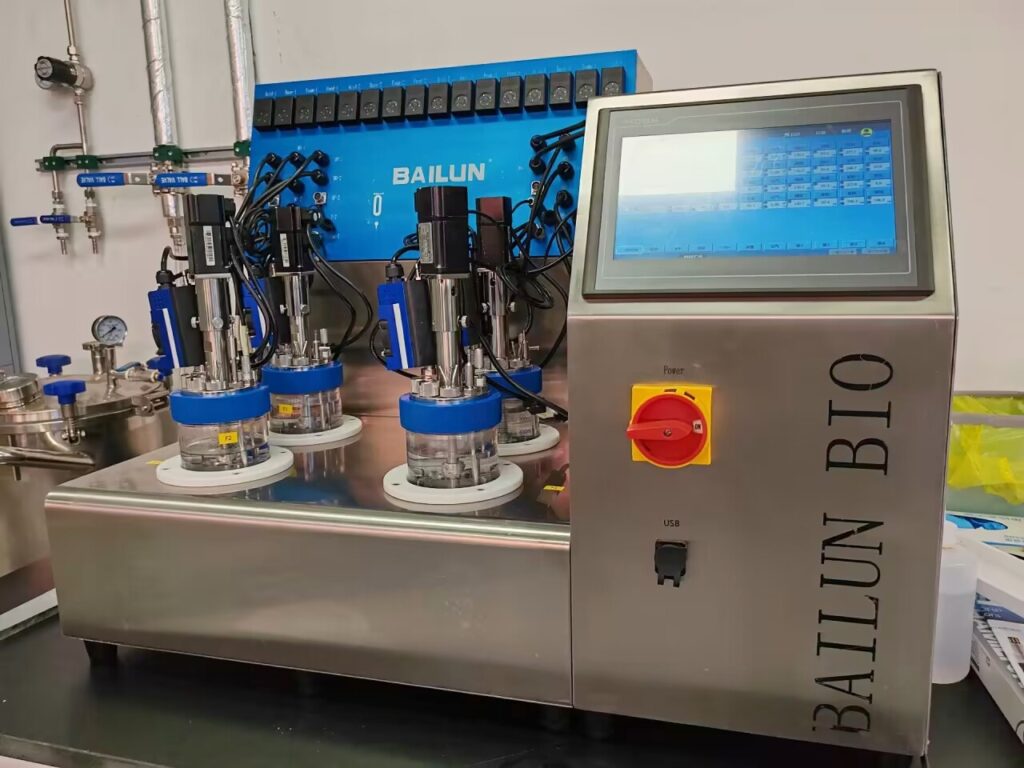
The micro pump is responsible for providing fluid pumping and controlling flow rate, the temperature control system is used to maintain a constant temperature inside the reactor, and the control system is used to monitor and regulate the progress of the reaction in real time. The micro bioreactor system has many advantages. Firstly, due to the small size of the reactor, it can reduce reaction time and substrate consumption, thereby improving reaction efficiency. Secondly, microfluidic chips can achieve precise control of reaction parameters such as temperature, pH value, and substrate concentration, making experimental results more accurate and reliable.
In addition, due to the small size of the reactor, multiple reactors can be run in parallel on the same experimental platform for high-throughput experiments, accelerating the progress of scientific research. Micro bioreactor systems have broad application prospects in fields such as biomedical, biopharmaceutical, environmental protection, and food industry. Through the application of micro bioreactor systems, researchers can delve deeper into the physiological characteristics of microorganisms, accelerate the development of new drugs, improve the efficiency of biological production processes, and develop new treatment methods and environmental monitoring methods.
Micro bioreactor systems typically consist of the following main components:
(1) Microfluidic chip of bioreactor system: Microfluidic chip is the core component of micro bioreactor system. It consists of a micrometer level channel network and microvalves. By adjusting the opening and closing of microvalves, the flow and mixing of fluids in microchannels can be controlled, achieving precise control of reaction conditions. Microfluidic chips are typically made of glass, polymer, or silicon-based materials.
(2) Micro pump of bioreactor system: A micro pump is a device used to provide fluid pumping. Micropumps are usually driven by pressure or electric means, which can achieve precise control of fluids. It can feed substrates, culture media, reagents, etc. into microfluidic chips to control the flow rate and fluid mixing degree inside the reactor.
(3) Temperature control system of bioreactor system: The temperature control system is used to maintain a constant temperature inside the reactor. Accurate control of reactor temperature can be achieved through heating elements and sensors. Temperature is crucial for the growth and metabolism of microorganisms, therefore the stability of temperature control systems is essential for the accuracy of experimental results.
(4) Control system of bioreactor system: A control system typically consists of hardware and software, used for real-time monitoring and regulation of the operation of a micro bioreactor system. It can monitor parameters such as temperature, flow rate, pressure, etc., and automatically adjust them according to preset reaction conditions. The control system can also record data during the experimental process and perform data analysis and processing.
In addition to the main components mentioned above, the micro bioreactor system may also include additional components such as sensors, detection instruments, and data storage devices. Sensors can monitor indicators such as biological activity, substrate concentration, and product generation in the reactor. Detection instruments are used to analyze and measure the quality and quality of the reaction process, while data storage devices are used to store experimental data and results.
The micro bioreactor system achieves precise control and efficient experimentation of microbial reaction processes through the combination of microfluidic chips and related equipment. This system has broad application potential in fields such as life sciences, drug development, and industrial production.
The micro bioreactor system has the following advantages:
(1) Small size: The size of micro bioreactor systems is small, typically ranging from micrometers to millimeters. Compared to traditional bioreactor system, microreactors have a smaller volume, saving laboratory space and allowing for the simultaneous operation of multiple reactors in relatively small devices. This small-sized design can also reduce the amount of samples and reagents used, lowering experimental costs.
(2) Rapid reaction speed: Due to its small volume, microreactors have a smaller reaction volume, allowing reactants to mix and diffuse more quickly in the channel, thereby increasing reaction efficiency to accelerate the reaction rate. Therefore, micro bioreactor systems can shorten reaction time, accelerate experimental processes, and improve experimental efficiency.
(3) Low sample and reagent consumption: The reactor volume in the micro bioreactor system is relatively small, resulting in a corresponding reduction in the required amount of samples and reagents. This not only saves expensive sample and reagent costs, but also helps to conserve scarce biological samples and valuable reagents in research.
(4) Accurate control of parameters: Microfluidic chips play a crucial role in micro bioreactor systems. Through the control of microchannels and microvalves, precise control of parameters such as reactant flow, temperature, pressure, and mixing can be achieved. This precise control can make experimental results more accurate and reliable, and provide more possibilities for optimizing biological reaction conditions.
(5) High throughput experiments: Micro bioreactor systems can achieve parallel operation of multiple reactors, known as high-throughput experiments. On the same experimental platform, multiple experimental conditions can be tested simultaneously, greatly improving the work efficiency and experimental output of researchers. High throughput experiments have important application value in drug screening, gene expression analysis, and other research.
(6) Integration and Automation: Micro bioreactor systems can be integrated with other devices and instruments to achieve automated operations. By connecting and coordinating with temperature control systems, liquid processing systems, detection instruments, etc., fully automated reaction process control and data processing can be achieved, improving the repeatability and stability of experiments.
(7) The micro bioreactor system has the advantages of small size, fast reaction speed, low sample and reagent consumption, precise parameter control, high-throughput experiments, and automation. These advantages make it an important tool widely used in fields such as biotechnology, life sciences, drug research and production.
Micro bioreactor systems have a wide range of applications in many fields. Here are some important application areas:
(1) Drug screening and development: Micro bioreactor systems are widely used in drug screening and development processes. By cultivating cells in microfluidic chips, the toxicity and efficacy of drugs can be evaluated. The small size and high-throughput characteristics of microreactors make it possible to test multiple drug samples simultaneously, greatly accelerating the speed of drug screening. In addition, micro bioreactor system can simulate drug metabolism and drug action in vivo, providing more accurate drug efficacy evaluation and dose optimization.
(2) Biopharmaceuticals: Micro bioreactor systems can play an important role in biopharmaceutical processes. By cultivating cell factories in microfluidic chips, efficient production and purification of biological drugs can be achieved. The precise temperature and fluid control capabilities of microreactors can optimize biological reaction conditions, improve production efficiency and output quality, and reduce production costs.
(3) Microbial research: Micro bioreactor systems are widely used in microbial research. The physiological characteristics and metabolic pathways of microorganisms can be simulated and analyzed on microfluidic chips, revealing the basic biological processes of microorganisms. Researchers can study the response and adaptation mechanisms of microorganisms to different environmental conditions by precisely controlling the effects of different factors such as temperature, pH value, oxygen concentration, etc. These studies can help deepen our understanding of the ecology, metabolic pathways, and evolutionary mechanisms of microorganisms.
(4) Environmental monitoring: Micro bioreactor systems can be used for environmental monitoring and pollutant detection. Through microfluidic chips, specific microbial strains can be cultivated to detect toxic substances, heavy metals, and pollutants in the environment. The sensitivity and rapid reaction speed of microreactors to microbial activity make them an efficient, accurate, and real-time environmental monitoring tool.
(5) Life science research: Micro bioreactor systems have also been widely used in life science research. Researchers can use micro bioreactor system to study biological processes such as cell signaling, gene expression, protein synthesis, and metabolic pathways. By precisely controlling reaction conditions, we can better understand the interactions between biomolecules, cellular functions, and mechanisms of disease development.
The application of micro bioreactor systems covers a wide range of fields such as drug screening, biopharmaceuticals, microbiological research, environmental monitoring, and life science research. The high throughput, precise control, and fast response characteristics of bioreactor systems provide researchers with an efficient, reliable, and innovative experimental platform.