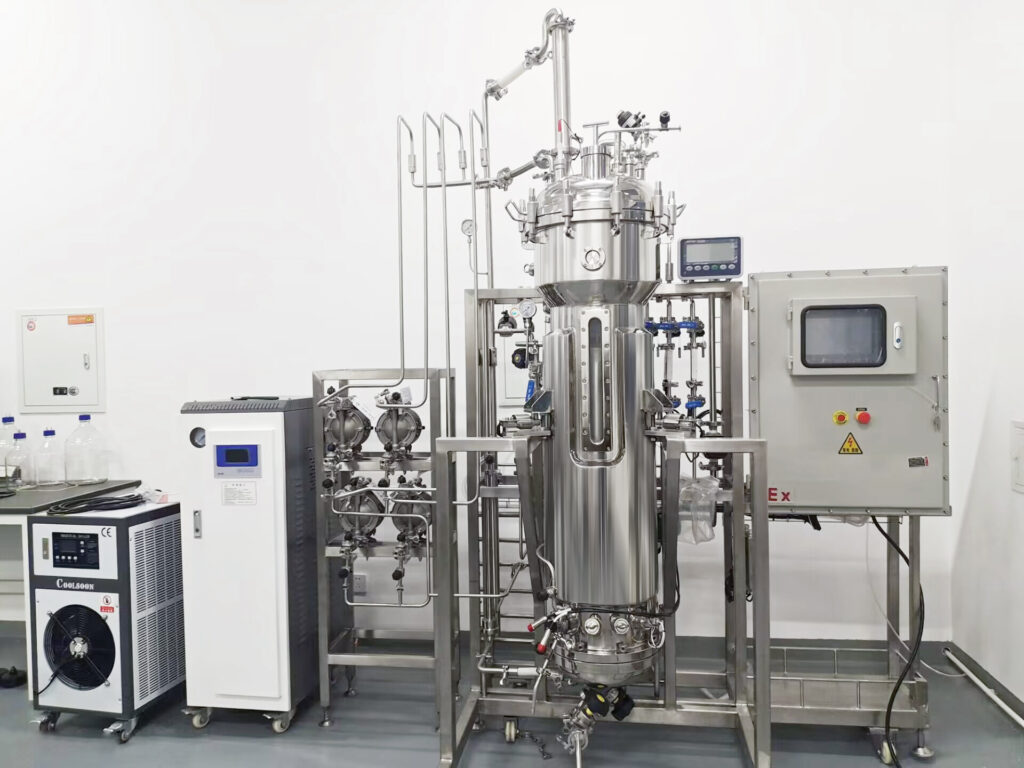
The airlift reactor is a revolutionary, economical, and efficient method that has set a new direction in airlift bioreactors in microbial processing. When we talk about airlift bioreactors, we mean a type of bioreactor that utilizes gas or air in the culture medium to create a flow that promotes mixing and oxygen transfer.
So, do you need efficient and effective biological processes like in wastewater treatments? Airlift bioreactors are thus a practical and sustainable approach to handling such. In water treatment they encourage the circulation of oxygen and thus lowering of the chemical oxygen demand (COD) and biochemical oxygen demand (BOD).
You will find out about how airlift reactors work in wastewater treatment and the essence of their creation in the following sections. This article also covers their design, advantages, disadvantages and other related areas.
What is an Airlift Reactor?
As pointed out, bioreactors are vessels used for cultivating biochemical life processes such as water purification and treatment in different areas – industrial, medical, or environmental.
However, most of you may not be aware that there is more than one type of a bioreactor that can be used for varying purposes. Well, we have an airlift bioreactor. This kind of bioreactor stirs up the culture medium by help of flow from compressed gas. The gas makes the liquid move around and this makes the nutrients and gases mix up well.
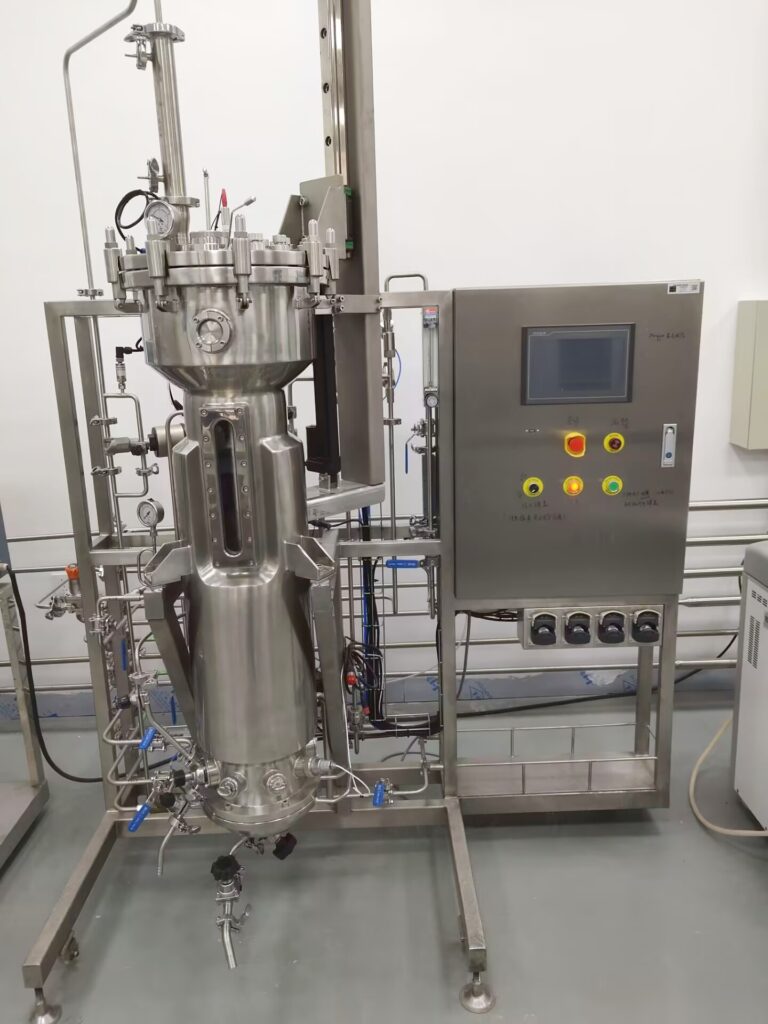
Types of Airlift Reactors
Airlift reactors are modern equipment applied in the field of water treatments and biotechnology processes. They also count on gas-driven liquid circulation to enhance the transfer/mixing treatment processes. There are two primary categories of ALRs:
1. External Loop Airlift Reactor (ELALR)
The External Loop Airlift Reactor comprises a riser and a downcomer which are two different but connected vessels that facilitate the movement of liquid.
The ELALR operates on the basis of density difference between the riser and the downcomer. This differential is made from the fact that in the riser only gas is injected. This makes the liquid move in a circular manner in a pattern that resembles a loop.
There is an incomplete gas disengagement at the top separator and this makes it possible for the External Loop Airlift Reactor in enhancing mixing as well as increasing the liquid flow. The outcomes are enhanced efficiency of liquid circulation. However, it has less gas recirculation and mass transfer compared to internal designs.
2. Internal Loop Airlift Reactor (ILALR)
Like the ELALR, the Internal Airlift Loop Reactor is a form of bioreactor made from two parts: the riser and the downcomer. The two parts are separated by a draft tube or a vertical barrier.
Well, there are more similarities in function of the ILALR and ELALR. For instance, a flow loop is created inside the reactor by injecting gas into the riser, much like in the External Loop Airlift Reactor. The Internal Loop Airlift Reactor’s small and effective design improves mass transfer by enhancing gas recirculation.
Besides, the Internal Loop Airlift Reactor is perfect for processes that necessitate a more enhanced contact between the gas and the liquid phase for its functionality. It is best in fermentation and biological wastewater treatment procedures.
Key differences between External Loop Airlift Reactor and Internal Loop Airlift Reactor
Feature | External Loop | Internal Loop |
Separation | External compartments | Internal baffle or draft tube |
Gas disengagement | Nearly total | partial |
Liquid circulation | Higher | Moderate |
Mass transfer | Lower | Higher |
Although both varieties of airlift reactors work well, they are selected according to the requirements of particular applications, including mass transport, mixing intensity, and space limitations.
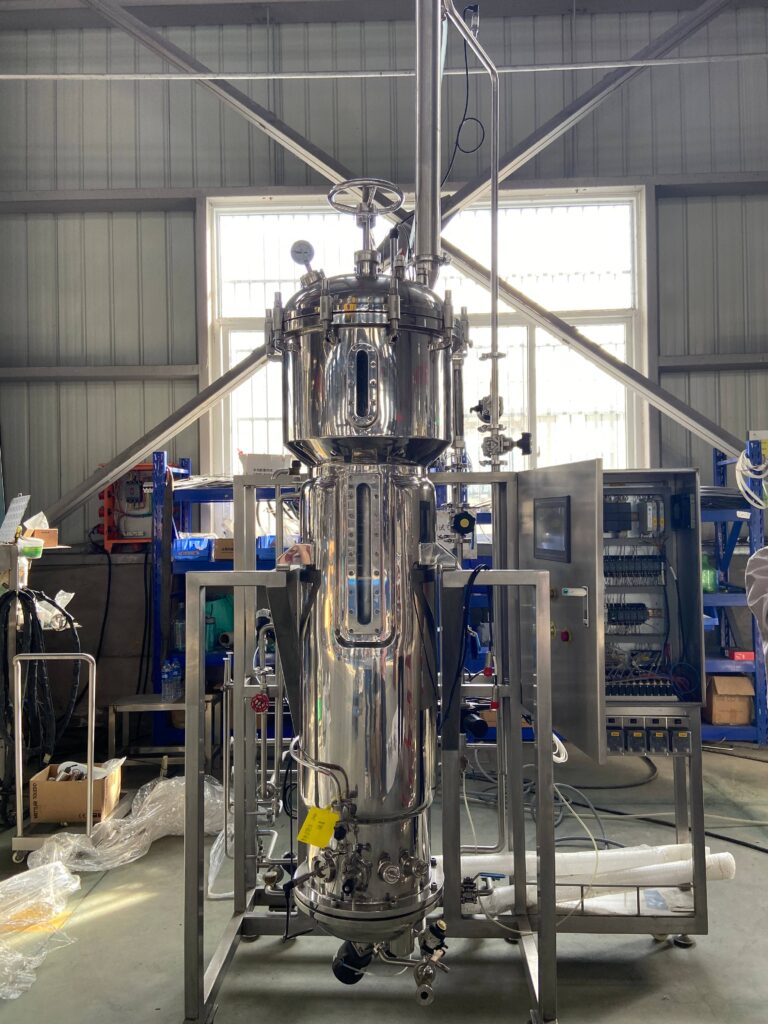
Airlift Reactors Design
The design of an airlift reactor greatly influences performance and efficiency. To comprehend the processes by which airlift fermentors and bioreactors function when treating wastewater, one must comprehend their construction and operation.
1. Basic structure
There are two zones in an airlift reactor — the riser and the downcomer. The riser is the point where gas is infused to cause an upward movement of liquid, on the other hand the downcomer provides a channel through which liquid flows down. Circulation is possible by the sensible height difference of these zones, maintaining a loop in the reactor.
2. Gas sparger
A gas sparger lowers gas into the system at the bottom part of the riser. The geometry of the sparger plays a central role in generating small gas bubbles which enhance mixing and oxygen transfer. The technique is most efficient where there are few bubbles. Generating many bubbles increases the surface area of the gas-liquid interface, making the process inefficient.
3. Internal or external loop
Depending on how their loops are constructed, airlift reactors can be divided into two primary categories:
Internal-loop reactors
These reactors possess a riser and a downcomer that is embodied in a single vessel. While this design is more compact and uncomplicated, it may not give a clear-cut separation as those seen in the external-loop systems.
External-loop reactors
In an external loop reactor, riser and downcomer are separate vessels or pipes.
While it occupies more space and can also be more expensive in the initial stages, this design allows you to have maximum control over the circulation and interaction.
4. Draft tube
Some airlift reactors have a draft tube installed inside them. A draft tube is a cylindrical structure that helps with circulation. Many designs place the draft tube in the path of the flow, which enhances the velocity of the upward and downward movement. Exclusion of stationary zones is particularly beneficial in internal-loop airlift reactors.
5. Liquid circulation control
The rate of circulation of the liquid depends on the volume of gas injected, height of the reactor and density of the liquid. Operators can then adjust these parameters to achieve high levels of mixing intensity as well as circulation speed if necessary.
6. Sensors and monitoring
You will realize that many contemporary airlift reactors have sensors to monitor variables like temperature, pH, biomass concentration, and dissolved oxygen. Operators can maintain ideal conditions for microbial activity and wastewater treatment using this data to guide their modifications.
Although airlift fermentors like the Multi-stage stainless steel 2000L industry fermenter are frequently employed in industrial settings to produce goods like biofuels and medications, airlift bioreactors and fermentors share similar fundamental design components. This design’s adaptability enables adaptation according to particular wastewater treatment objectives.
Utilizing Airlift Reactors to Treat Wastewater
Airlift reactors exhibit flexibility and adaptability in a variety of industries by being used in a broad range of wastewater treatment scenarios:
1. Municipal wastewater treatment
Some of the organic pollutants found in municipal wastewater include phosphorus and nitrogen. The microbial populations necessary to remove these pollutants are sustained by airlift reactors. They are economical for large scale municipal plants due to energy favorability and high oxygen transfer rates.
2. Industrial wastewater treatment
The specific sector that generates wastewater rich in biochemical oxygen demand includes chemical, food processing, and pharmaceuticals industries. Such effluents can be efficiently treated by modifying airlift reactors, especially the external loop ones. Due to its high biomass content, complex organic compounds break down more in these types of reactors.
3. Nutrient removal
Water bodies become contaminated and eutrophic through nutrient imbalance, especially Nitrogen and Phosphorus. Airlift reactors also enable the removal of the above nutrients as the system harbors microbial communities that fix the issue.
4. Anaerobic treatment of wastewater
Airlift reactors can be made to function with no oxygen. The main advantage of anaerobic methods is that it can produce biogas that can be used as a source of energy. This is beneficial in the treatment of wastewater with high BOD and COD values.
5. Treatment of toxic waste
Some toxic chemicals found in certain industrial wastewater negatively impact normal aerobic bacteria. Airlift reactors are still safer as well as a more effective treatment mechanism involving the use of dedicated microbial consortia for the degradation of these toxic compounds.
6. Volume reduction of sludge
Sludge is observed very often as a final product of wastewater treatment, and its removal is a problem. The airlift reactors degrade organic matter in a more efficient manner and result in less sludge production, easing disposal.
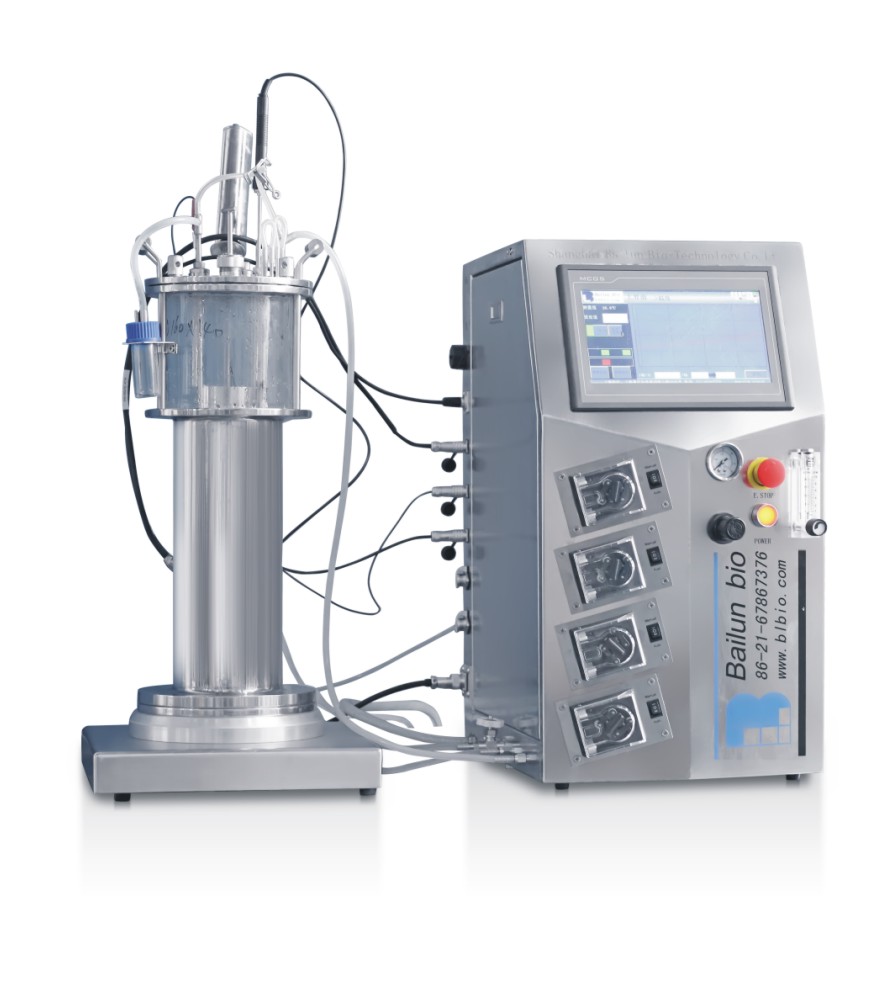
How Do Airlift Reactors Work in Wastewater Treatment?
You are probably wondering how airlift reactors function. Basically, air is introduced into a draft tube, creating bubbles that transport liquid to the top. This gives rise to a closed circulation pattern due to continuous upward flow of liquid. Below is a detailed look into how airlift reactors work:
1. Aeration and mixing
In the reactor’s riser section, air is supplied. As the gas rises, the liquid in the riser moves upward, and the downcomer then flows downward. Because of the extensive mixing provided by this circulation, the reactor’s gasses and nutrients is distributed evenly.
2. Microbial decomposition
Wastewater includes organic matter that microorganisms feed in a specified reactor. This process reduces the chemical and biochemical oxygen demand (BOD and COD).
3. Sludge separation
After the microbial treatment phase, some of the biomass falls and is deposited at the bottom of the reactor. When treated water advances to the next level of purification, the settled biomass or sludge can be easily scooped for more treatment or disposal.
Airlift Reactors’ Benefits for Treating Wastewater
Airlift reactors are popular for a variety of applications because they provide a number of benefits in wastewater treatment:
1. Effective oxygen transfer
As we have noticed, there is always counter current circulation in the riser and downcomer zones. As a result, airlift reactors offer high oxygen transfer compared to stirred tank reactors.
Have you worked on aerobic wastewater treatment systems? If so, you should know that effective gas transfer is necessary for all aerobic treatment techniques because oxygen is essential to microbial processes.
2. Reduced energy needs
Relative to other reactors, airlift reactors are also relatively energy efficient since mechanical stirring is not necessary. Since most of the process is about the circulation, there is a slow down in the use of energy and operating cost.
3. Improved mass transfer and mixing
An important feature of airlift reactors is the capability to provide full mixing throughout the reactor so as to eliminate dead zones that would negatively affect reaction kinetics. For wastewater treatment, this makes them very effective since the process depends on consistent gas and nutrient dispersion.
4. Minimal shear stress
Mechanical stirring can be destructive to the microorganisms in industrial scale bioreactors where microbial viability is important. Microbial growth and efficacy for pollutant removal are upgraded by the relatively favorable conditions and less shear stress.
5. Application flexibility
Owing to the flexibility, airlift reactors are used for any biological process of interest. They are particularly suitable for wastewater treatment in aerobic and anaerobic conditions. It is equally suitable for treating industrial water and effluents.
6. Decreased maintenance required
Airlift reactors also have less mechanical design than pumps. For this reason they are less complicated than other types of reactors, making them easier to maintain.
Airlift Drawbacks
Airlift reactors have the following drawbacks that may reduce how well they treat wastewater:
1. Limited gas retention
While you’ll enjoy the efficiency of oxygen transfer in airlift reactors, there are circumstances when the amount of gas that can actually be held in the liquid is limited. As this goes on, oxygen supply may reduce especially in activities that require high energy. Eventually, this may affect the overall efficiency of the microbes.
Do you undertake large scale wastewater treatment? If yes, then the airlift reactors may not be a perfect match. Airlift reactors perform efficiently with a modest scale of wastewater treatments. Sustaining the right mixing and circulation needed in such systems becomes difficult as the system expands.
2. Greater initial investment
The construction costs of airlift reactors are likely to be higher than those of conventional pumps due to the need for special materials and construction techniques. Despite realizing cost savings on operation, the investment costs on the equipment could be a limiting factor especially to small facilities.
3. Possible clogging
Airlift reactors may easily get blocked in wastewater application containing suspended particulates. This increases the need for close monitoring and possibly other subclass filtering procedures.
4. Viscous fluids
For highly viscous wastewater, the performance of airlift reactors is low. Why? The circulation of the gas-liquid can be interrupted by the viscous fluids, reducing the efficiency of the treatment.
Other Methods of Treating Wastewater
Treating wastewater can be achieved with many technologies based on the kind and concentration of contaminants to be removed, the treatment goal, and the cost factor. The options include:
1. Physical treatment methods
Screening is frequently the first step in wastewater treatment, where big particles like plastics and rags are removed by mechanical screens. After that, suspended solids are allowed to naturally sink to the bottom of sedimentation tanks so they can be removed. Lastly, filtration techniques like sand filters, activated carbon, or sophisticated membranes remove pollutants and tiny particles to guarantee clearer water.
2. Chemical treatment method
This method involves the use of chemicals like ferric chloride or alum. Coagulation and flocculation form the initial step and involve adding substances such as alum or ferric chloride in order to group small particles.
Chlorination or UV light or ozone treatment are then employed to kill all types of pathogenic organisms.
Finally, by adding materials like lime, soda ash, or acids, pH adjustment balances acidic or alkaline water and guarantees that it meets safe drinking requirements.
3. Biological treatment
For biological treatment, the organic pollutants are minimized by microbial cultures or aeration tanks. The pollutants are reduced by biofilms as the wastewater passes through a bed of the media.
This treatment involves constructing wetlands. The wetlands mimic natural wet environments, where plants and microorganisms are used in the water filtration process.
4. Anaerobic treatment system
Anaerobic treatment systems are capable of degrading organic pollutants once there is no oxygen available. For instance, anaerobic digesters discharge biogas in the process of treating trash.
Furthermore, high strength industrial effluents often undergo treatment in Upflow Anaerobic Sludge Blanket (UASB) reactors. These reactors are a good investment because they are able to control waste and even generate power.
5. Emerging and hybrid technologies
A number of cutting-edge technologies are improving the effectiveness of wastewater treatment:
- Moving Bed Biofilm Reactors (MBBR): These reactors greatly improve treatment efficacy by promoting biofilm formation using floating media.
- Photocatalysis: This method breaks down contaminants by using catalysts and ultraviolet light, providing a hygienic and effective treatment option.
- Nanotechnology: Toxins and trace pollutants are eliminated using sophisticated filters and adsorbents created using nanotechnology, eliminating contaminants that conventional techniques could overlook.
Conclusion
Airlift reactors are a cutting-edge method of treating wastewater because they combine sustainability, flexibility, and efficiency. They are handy for biological wastewater processing because their unique design improves mixing and oxygen transfer.
Even though they have certain drawbacks, airlift reactors’ benefits frequently exceed the drawbacks, especially in applications where delicate mixing and energy efficiency are crucial.
In a time when the need for clean water is greater than ever, innovations like the airlift fermentor and bioreactor present viable options for sustainable wastewater management. So are you looking for solutions to wastewater treatments? Check out our reactor — we provide overall solutions to wastewater treatment.